54000KVA全密闭型电石炉在生产中的管理创新与技术改造应用
甘肃金泥化工有限责任公司 党总支书记、董事长 刘培雄
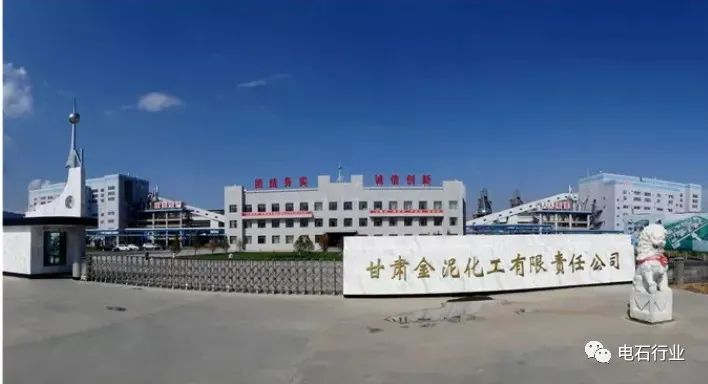
甘肃金泥化工有限责任公司(以下简称:金泥化工)54000KVA全密闭型电石炉是由金泥集团公司、中国天辰工程有限公司、中钢集团吉林机电设备有限公司联合开发,是国内自主开发设计的大型全密闭电石炉,金泥化工电石生产线于2013年建成,2017年7月1#电石炉首次送电试生产。
一、基本情况及应用方案
金泥化工54000KVA大型密闭电石炉为新开发炉型,电极系统采用南非麦迪克斯技术,三相电极为自焙烧电极。项目竣工后设计院没有可参照的作业指导书,只能自行探索总结工艺参数和操作经验。生产工艺没有经过实践验证,工艺技术参数核算不精确,试生产过程没有强有力的技术团队,同行业没有可有效借鉴控制方案,在初期运行中只能靠个人经验来判断,电石炉无法做到连续稳定生产。且电极直径大,埋入量无法有效控制,电极长度没有精确测量手段,三相电极做功不平衡,三相熔池很难有效贯通,电石炉经常出现塌料、喷炉等,这些因素严重制约了电石炉产能的提升。针对这些现状,金泥化工积极探索研究,从基础管理、工艺管控、设备专业化检修入手,不断探索新技术,大力推进智能化、机械化升级改造,电石炉生产不断向好,产量逐步提高。1.为稳定生产,进一步提高电石炉产量,金泥化工成立电石炉产量提升攻关小组,在确保安全生产的基础上稳步提升电石炉负荷,保证公司整体产能的不断提升。2.始终坚持以“高配比、高炉温、高负荷”为生产理念,以“降电流、提电压、提高功率因数”为操作方法,以智能化、机械化为手段,以能耗、质量为切入点,以运转率为保证,全面落实“间歇生产连续化,连续生产稳定化”的生产理念。改变操作理念,贯彻落实“稳产就是高产”,杜绝班组挖产,促进电石炉安全稳定运行。坚持目标导向,想方设法解决实际问题,从原料各项指标分析开始,及时调整各项工艺参数,保证三相电极平衡,达到持续稳定生产的目标。 3.强化“三班保一炉”操作理念。为保证电石炉稳定运行,蓄热炉温,制定“三班保一炉”操作理念,平衡出炉,做到负荷与产量匹配,配比与质量平衡,通过控制单耗,保证电石炉持续在高炉温下稳定运行。4.面对石灰石资源紧缺,周边石灰石矿产资源不适宜电石生产,热爆性高、煅烧成品生石灰粉末率大等问题,不断摸索、验证和实践,制定了适合金泥化工54000KVA电石炉生产的石灰石搭配比例,进一步稳定了电石炉生产。5.加强电极管理。在生产实践中不断完善《金泥化工54000KVA电极焙烧方案》《金泥化工54000KVA停送电操作规程》,并与电极糊生产厂家沟通,对电极糊配方优化调整,保证电极焙烧和消耗相匹配,保证了电极的质量,杜绝了电极事故的发生。6.引入智能化、自动化控制系统。电极智能控制、电极测量、温度测量等自动化管理,校企联合,研究解决制约电石炉生产的“卡脖子”技术。目前4台电石炉已全面开展电极智能控制系统运行,下一步持续开展机械化、自动化、智能化控制系统的应用,找突破,严要求,切实解决电石炉操作不统一、影响电石生产连续稳定运行的问题。1.不断完善安全管理制度,始终保证以人的安全为中心,风险管控为重点,强化职工安全教育培训,岗前确认、班组日检、车间周检以及班前以“一岗一承诺”的形式,明确各岗位安全职责,危险辩识及安全防范措施,严格执行电石生产操作组织实施方案,提高各岗位人员安全意识,杜绝人的不安全行为,防止安全事故的发生。2.定期召开电石生产分析交流会。定期组织相关技术人员召开电石生产分析会,集思广益,找不足、补短板,总结操作经验,继续加强生产组织管理和工艺运行参数统计分析,力求达到三相电极的平衡,最大限度克服解决电极管理短板,确保电石炉长周期稳定运行。3.完善54000KVA电石炉工艺控制方案。对电石炉稳定运行期间的数据收集整理,分析总结适合54000kVA密闭电石炉的运行参数,形成数据库;总结完善《金泥化工54000KVA作业指导书》《金泥化工负荷与压放时间控制方案》,通过勤对比、微调整,将理论和实践结合起来,从运行参数中找基准点,调整控制参数,做好组织管理和生产衔接,电石炉生产稳定向好。4.保证原燃材料的质量安全。成立原材料验收小组,严格按照先验后卸的原则,保证原燃材料质量安全,为电石炉的稳定运行创造有利条件。同时加强中间产品质量过程控制,建立健全考核奖励制度,修订《生石灰、兰炭质量考核规定》,健全中间产品质量管理制度,保证中间产品质量,确保电石炉正常稳定生产。在生产过程中,净化系统布袋入口温度高,电石炉负荷只能提到70%,造成三相熔池无法打通,严重制约电石炉稳定生产。针对这一问题,金泥化工结合现场实际情况,通过理论计算换热面积,而原设计的两台旋风冷却器和一台多管冷却器冷却面积严重不足,经与设计单位沟通印证,最终达成一致意见,制定改造方案:拆除原有旋风冷却器和多管冷却器,更换为三台串联的空气冷却器,冷却形式均由以前的强制冷却变为自然空冷。目前,四台电石炉净化冷却器均已改造完毕,正常生产过程中布袋除尘器入口温度可控制到220℃左右,为电石炉安全生产提供了保障。金泥化工4台54000KVA电石炉全部投运时,每天要产生粒度小于等于8mm的石灰粉末,不能入炉参与电石生产,极大的降低了原材料利用率,为使该部分高品质石灰得到充分回收利用,通过多地考察、仔细论证,新建一套石灰粉压球生产线,将石灰粉末进行综合利用,大大降低了生产成本。电石炉在生产过程中,出炉岗位作业环境危险、劳动强度大、人员流失严重,人工出炉作业方式,存在很大的安全隐患,严重威胁了一线员工的生命安全。针对这一情况金泥集团与哈尔滨博实自动化股份有限公司联合研发应用于54000KVA电石炉的专用出炉机器人,重点解决炉前烧炉眼、开眼、带钎、堵眼、清炉舌等工作,目前出炉机器人应用效果好,不仅降低了员工劳动强度和安全风险,也为电石炉高负荷生产打下了坚实基础。
4.电石炉炉盖系统优化改造
电石原炉盖不锈钢盖板部分由1块中心盖板、3块相间盖板、3块外围盖板共7块拼装而成。炉盖共设14个吊挂,外围11个,中间3个。7块盖板均靠14个吊挂垂直悬挂定位安装。改造后取消原有炉盖底部环形梁结构,减少迎火面焊缝,同时将炉盖数量优化成6块,降低了炉盖烧损漏水几率和维修难度。在炉盖上表面电极孔周围焊接水冷套增加炉盖强度同时为电极密封提供可靠支撑。炉盖底部浇筑80mm厚的高铝浇注料(耐温高达1600℃),配套“羊角形”不锈钢锚钩,对炉盖起到良好的保护作用。
5.电石炉加料系统优化改造
经过考察论证,设计订做环斗加料机置换原有的环形加料机。环斗加料机由环形车体(料斗)、环形轨道、开门装置、关门装置、环形集尘罩、传动系统、顶紧装置等组成。现场就位后六瓣拼装焊接成为一个完整的环形车体。环形车体外侧安装柱销,与传动系统大齿盘啮合通过边缘传动使环形车体在底部环形上转动运行。料斗底板为活动底板,可绕一侧固定轴旋转。每个料仓设置一个气动开门装置,当料仓求料时,对应气动开门装置气缸顶出打开运行至该料仓上部的料斗底板,使物料落入料仓。料斗运行至其受料点前,通过闭门装置关闭料斗底板再次受料,实现周而复始的加料过程。
6.电石炉下料管升级改造
金泥化工54000KVA电石炉共16根下料管,中心料管和边缘料管均为直圆柱形,边缘料管为折弯圆柱形,其中部朝电极侧设计垂直偏移15°的折弯角度,目的是使落料点更接近电极。在应用实践中发现,边缘料管底部距三相电极表面水平距离偏大,通过边缘料管进入炉内的物料堆积零散不集中,不能紧紧“包裹”三相电极形成理想的物料堆积形式。造成料层结构差、埋弧效果不良、电极热损失大、料面板结、支路电流增大等一系列不良反应,进而影响电极埋入量、电极电流、单耗的有效控制。针对此情况,经过分析研究,对原边缘料管进行了设计优化,把以前的“折弯形”料管改为“圆弧形”料管。改造后的边缘料管底部更接近电极,落料点距电极表面水平距离缩小。投入使用后,效果明显,入炉物料在炉内能紧密、均匀包围在三相电极周围,形成理想的“馒头状”物料堆积形式,提高了热能利用率,降低了支路电流,完全达到了预期的改造目的。对电石炉炉舌、炉门框、炉壁进行优化升级,通过考察论证,与专业检修队伍共同制定检修方案,吸取高炉炉壁修复技术,结合电石炉炉墙特点,利用高压压注设备,将耐高温刚玉压入料填充到炉壁和耐火砖之间,外壁采用加强筋板,以及采用水冷壁进行冷却,大大提高炉壁使用寿命,目前运行效果良好。金泥化工54000KVA电石炉采用中压电容并联补偿方式,在正常投用过程中,对变压器补偿线圈产生过电压冲击,时刻威胁变压器的安全运行,为此金泥集团通过高压、中压、低压等不同无功补偿方式比较,结合现有特种变压器三线圈功能,经过现场调研、测试、理论计算,合理选择动态无功补偿(SVG)+现有电容补偿装置(FC)组合方式,改造后可实现无极平滑投切,动态响应时间10ms,能进行单相分补,其自动化程度高、维护量少,安全性高,基本解决了变压器补偿线圈受过电压冲击的问题,实现了平滑无扰动调整。综上所述,通过加强管理,职工素养得到提升、思想得到统一,为稳定生产打下基础;通过加强工艺方面的管理,电石炉生产趋于稳定,产能大幅提升;通过设备改造和专业化检修,设备运转率大幅提升,连续运行时间由原来的的7天提高到20天以上。通过智能出炉机器人的使用,出炉工劳动强度大幅下降、危险性降低、人员流失情况得到改善;加之智能电极控制系统的研发与应用,电石炉做功明显好转。通过以上创新技术的实施,电石炉产能大幅提升,单台炉电石产量突破8060吨,功率因数由之前的0.84大幅提升到0.9以上并趋于稳定,工艺电耗稳步控制在3200Kwh/吨以内,电石炉生产持续向好,能耗逐步降低。金泥化工54000KVA全密闭电石炉为新开发炉型,目前国内未形成较成熟的工艺控制方案。金泥化工公司通过管理提升、工艺优化、操作完善、设备升级改造等方式,使电石炉运转率大幅提升,生产持续向好。同时坚持以“安全为底线,质量为基础,能耗为目标,运转率为保证”的理念,贯彻执行“间歇生产连续化、连续生产稳定化”操作办法,在生产组织管理、电极操作、压放时间、配比调整等精细化操作上持续保持前瞻性、及时性,主动寻求稳定电石炉生产操作法,切实做到提产增效,节能降耗,实现电石炉长周期稳定运行,助力电石产业向更高的绿色发展目标迈进!(编辑:蒋顺平)